Panduan Cara Main & Daftar Situs Slot Gacor 2024
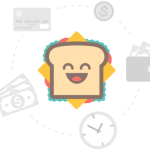
Panduan Cara Main & Daftar Situs Slot Gacor 2024 – Judi slot online terbaik mudah menang dan terpercaya hadir sekarang untuk membuat kamu merasakan keuntungan besar semakin berlimpah sebagai pemain baru. Jika kamu tertarik untuk mencoba bermain taruhan pada situs judi slot terperpercaya tentunya kamu tidak harus khawatir akan kekalahan…